The Process FMEA is so useful… and so poorly conducted a lot of the time.
There is an art to it, just like there is an art to conducting a solid root cause analysis. It seems to be quite a difficult and unnatural exercise for most engineers, technicians, and managers in China or Vietnam.
What is a process FMEA (pFMEA)?
The pFMEA is a formal approach to proactively reducing risks in a process.
A failure modes & effects analysis (FMEA) aims at:
- Identifying potential risks
- Documenting and keeping track of those risks
- Sorting those risks highest to lowest, and focusing more attention on the highest sources of risks
- Driving corrective actions that will contribute to an overall risk reduction
- Keeping track of the status and the impact of these corrective actions
When to work on the pFMEA?
If you already have a mass production running, you can start to analyze risks and add controls where they are needed. Right away, without waiting.
If you are developing a new product, the pFMEA may not be the first step in your risk analysis. The logical steps are usually as follows:
- Plan for the product requirements, based on who will use it, what the general purpose is, what the use environment will be, etc.
- Do a user FMEA and refine as needed
- Plan for the product design (what form factor, what features, what finishing, etc.) that is needed to satisfy the product requirements
- Do a design FMEA, make prototypes and test them, and iterate & adjust as needed
- Plan for the manufacturing & testing processes that are needed to make the product as it is designed
- Do a process FMEA, introduce controls and improve the process where needed, run pilot validation tests, and improve & adjust as needed
It is nicely represented in this graph:
Image source: Risk Management for Medical Device Manufacturers, by Joe Simon
What other tools do we use a process FMEA in conjunction with?
Applying an FMEA to a production process is quite helpful. When there are serious quality issues coming from multiple sources, our consultants tend to follow this sequence:
- Mapping the process (in the form of a flow chart)
- Working on an FMEA analysis of the process with the factory staff (by simply following the steps mapped previously and wondering, ‘what can go wrong or has gone wrong’?)
- Filling out a process control plan to document and standardize the controls — both those already in place, and new ones implemented as responses to the highest sources of risks shown in the FMEA.
(Steps 2 and 3 are quite interrelated and are usually done in parallel.)
Doing a process FMEA is also a great component for a new product introduction (NPI) process. Many companies skip it but it really adds value when an entirely new product is developed. It is a compulsory part of the PPAP (what I would call ‘NPI 2.0’, for makers of OEM auto parts).
Where to get a good pFMEA template?
A good process FMEA template can be downloaded on the Gemba Academy website. There are many others but this is the one we have used as a basis for our company’s template. It is relatively simple and it works.
An important note, however, is that, depending on the industry, companies are NOT free to pick any template they want. The template I suggested above is OK in general, but may not be adapted for companies in the automotive or medical space.
For example, for the manufacture of automotive parts, they should refer to the AIAG/VDA FMEA Handbook. For medical devices, the US FDA refers to standard IEC 60812. In such highly regulated industries, it’s very important to follow the requirements.
If you make general consumer goods, you have much more freedom. Remember, the value of a good pFMEA is to have all the important sources of risk in mind so they can be addressed.
What is most important when filling out the template?
First, try to think of many potential failure modes. If you forget a failure mode that carries a high risk, you won’t work on preventing it, detecting it early, or reducing its impact… Don’t go too fast here. Ask people who come from different teams/departments what could go wrong (and show them a few pFMEA examples, to jump-start the exercise). Their different perspectives will help a lot.
Second, if you are not in mass production yet, take a quick pass at estimating the likelihood, severity, and detection. Don’t spend a lot of time debating whether it is a 4 or a 6…
Third, spend some time working on the ways to reduce those risks. That’s where you will reap the full value of this exercise. Without it, it’s all useless…
How to fill it out?
The columns most to the left show the potential issues (‘failure modes’) identified and their impact.
Then, each potential issue is rated on the 3 dimensions of risk:
- How severe is it, in case if happens? (‘Extremely severe’ is a 10)
- How likely is it to occur? (‘Certain’ is a 10)
- If it happens, how likely is it to impact the customer, rather than being caught internally? (‘Certain to get to the customer’ is a 10)
(Click on the image to enlarge.)
At this stage, the potential issues can be sorted — highest risk on top.
After that, how to tackle the sources of highest risk? By analyzing root cause(s), thinking of corrective action(s), implementing those actions, following up to ensure those actions are effective, and re-evaluating the risk level.
The best organizations do this exercise regularly. They gather information, take action, and update the process FMEA risk scores. And again. And again.
Common issues with FMEAs
Many failure modes that result in high risks are generally omitted. People tend to overlook some of these aspects: safety, form fit, function, and material concerns.
Another issue is, past issues are not taken into account. Actually, past issues on the same or on a relatively similar process are a great starting point for an FMEA!
Here is a longer list of common issues (coming from New Tricks for an Old Tool, published in Quality Progress in May 2017):
The reverse FMEA
An FMEA has to be reviewed and updated regularly based on real data.
It has become a bit of a trend in the automotive industry, and several OEMs have made it compulsory since about 2020.
Basically, it is a review & adjustment process (where most companies are really weak). Once the FMEA, the CP (control plan), and the WIs (work instructions) are in place, they need to be reviewed for adequacy and effectiveness over time, but most companies don’t do it systematically.
FMEA is prepared looking forward, it is preventive in nature. For example, probabilities are estimated (often without historical data on comparable products/processes) and may be way off; some failure modes may not be well described; etc. And the FMEA analysis is a foundational exercise that shapes the way MFG & testing processes are implemented, where controls are added, etc.
But, over time, as the process is underway, it is good to confront the FMEA to reality with a reverse FMEA. It is basically a process of reviewing & adjusting.
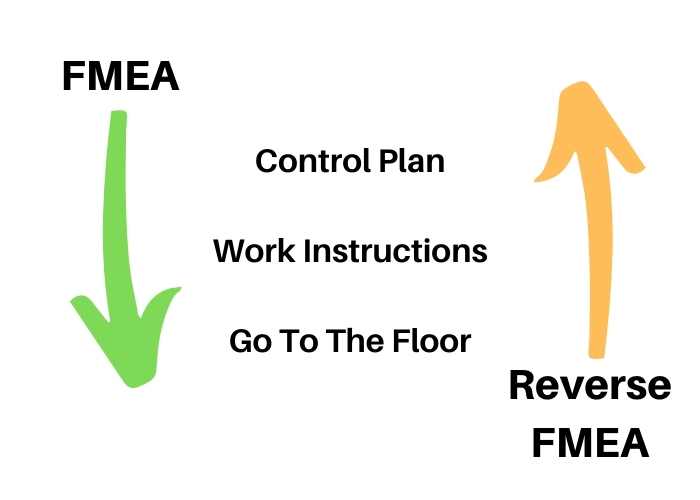
It is also good to review the reverse FMEA analysis with a team (with members from manufacturing, purchasing, process engineering, quality…) and adjust it. Similarly, the CP and WIs may no longer be current! They need to reflect the reality of what is happening and what risks need to be prevented/detected.
(Note: Ford Motors has started to require RFMEA when new equipment is designed and when it is put in place, not only after production launch. That makes sense, and more and more companies will also start to do that.)
Process FMEA examples
Here are a few examples of pFMEAs. The key sections have been filled out and I talk you through each part so you understand how these analyses work in practice.
Wooden toy assembly & packing process
Watch the video here.
Wooden toy drilling process
Watch the video here.
Wooden toy painting process
Watch the video here.
Note: the example of scoring sheet shown in the video can be downloaded here. Remember, it’s just an example, and you may need to adapt it to your needs!
******
What do you think? What have your experiences been with process FMEAs? Let me know by commenting on this post, or contact me.
Editor’s note: This post was originally published in 2017 and has been updated with new content in September 2022.
The New Product Introduction Process Guide
In this guide, we explore everything that inventors, SMEs, and hardware startups need to know about making a new product in China and bringing it to market.
We include:
- Why preparation between product design and launch is necessary
- Exploring the NPI process, from product idea to production
- Finding the right manufacturing partner
- Design reviews & adjustments: DFM, DTC, DFQ
- Optimizations for improving cost and quality
- Small production runs before mass production
- Your role in the NPI process
If you’d find this helpful, take a look now over at Sofeast by hitting the button below: