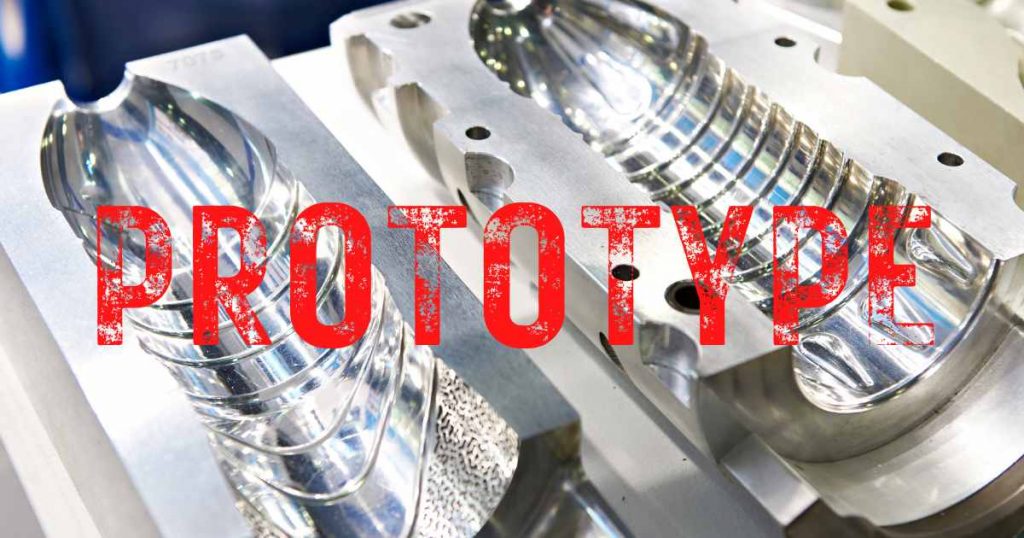
I had a look at Kickstarter today and I saw a few examples of such products. It’s likely that the companies behind these three products have to put a lot of money down on various types of tooling.
And it always sparks legitimate questions such as ‘can’t we just use prototype injection molds for the first production run?’. Unfortunately, it’s not that easy.
Why the jump to production molds is a bit uncomfortable
In The Conundrum of Investing in Tooling Before a Final Prototype, I described a common situation and the issues it leads to:
A typical situation when investing in tooling is required
After a prototype is approved, companies are often faced with a conundrum.
- If the product includes a plastic casing, for example, the casing of the prototype was certainly prepared without tooling. It was made by additive manufacturing (i.e. ‘3D printing’) or by cutting matter away from a block of plastic (i.e. CNC machined). But that’s NOT the process that will be followed in mass production.
- All that means is, production will NOT be 100% similar to the prototype. (There may have to be a gate mark, a part line, and so on, on the pieces coming out of injection molding.) The approved prototype means product design is confirmed, but it is NOT the “golden sample” yet.
Not having tooling will hold back key approval steps
Without tooling, certain key approval steps cannot take place yet:
- Testing for certifications
- Reliability testing
- Final approval of what production will look like
And that means the company financing the development and manufacturing of the new product is facing a gap they have to jump over. It is never an easy decision.
Any prototype injection molds and techniques that may make sense?
To get to the point where a nice-looking and functional prototype is put together? Yes, sure.
To make 30 samples that will be used for compliance and reliability testing? Sometimes, not always.
To make a first production run of 500 pcs? Seldom — at least in China.
We drew a list of rapid prototyping methods before, and we put together a nice cost comparison table. Let’s cover this topic here, with a few rules of thumb:
- Silicon molds: good only for about 25 pcs of each part, and the unit cost of 1 part will be about 10 times higher than with a steel mold.
- Load blocks of plastic in a CNC machine that will remove some of the matter: each part will typically cost 20 times more!
- 3D printing: definitely not viable for certifications, or for reliability testing. The parts’ physical properties, and aesthetic aspects, are markedly different from those coming out of injection molds.
- Softer metal (e.g. aluminum) molds: do not compare favorably to steel molds. In China, the cost is about the same, so of course, you should go for tooling in steel, which will ensure a longer lifetime.
Now, you might ask, what if the design may have to evolve a bit? Steel tooling does allow for some changes in certain dimensions, so it does give a bit of flexibility.
In addition, all those “prototype injection molds” will shape parts without the great level of precision characteristic of steel tooling.
The bottom line…
For all those reasons, we always push our clients to do proper design reviews and prototype testing, and then to make the jump to steel tooling — generally to hard steel directly. There are exceptions where that doesn’t make sense of course, but we haven’t seen many such exceptions so far…