What Does AQL Mean?
‘AQL‘ stands for ‘Acceptance Quality Limit‘, and is a method used by many businesses to check a random sample from the production batch of their products and confirm that the risk of bad quality is relatively low.
In ISO 2859-1, the AQL is defined as the “quality level that is the worst tolerable.” It represents the maximum number of defective units, beyond which a batch is rejected. Importers usually set different AQLs for critical, major, and minor defects. Most Asian exporters are familiar with this type of setting.
For example: “AQL is 1.5%” means “I want no more than 1.5% defective items in the whole order quantity, on average over several production runs with that supplier, and I accept a certain amount of risk that I make the wrong decision based on the imperfect information coming from checking only a sample of the whole batch”.
Table of contents
Use these links to jump to the different sections of this article:
- What are the AQL Tables? (including video explainer)
- Convenient AQL calculator
- A more detailed look into the AQL
- Special case: the AQL in the Codex standard stan233 (food products)
- FAQs
Getting familiar with the “AQL tables”, sometimes called “ANSI tables”
The “AQL tables” are statistical tools at the disposal of buyinspection levelers (for product inspections). They are an industry standard. Most suppliers involved in international trade are familiar with it.
They help determine two key elements:
- How many samples should be picked and inspected, among a batch of product or parts?
- Where is the limit between acceptability and refusal, when it comes to defective products?
This video will help you become familiar with how the AQL tables work and are used:
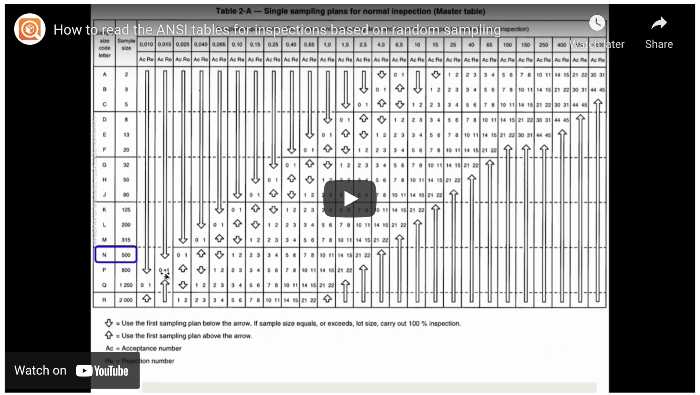
Before using the AQL tables, you should know three parameters:
1. The ‘lot size’
If you ordered different products, consider each product as a separate lot. (The quantity of each product is the lot size). If you ordered only one product, the lot size is the total batch quantity.
2. Inspection level
Different inspection levels will command different numbers of samples to inspect. In this article, we will stick to the so-called “level II” under “normal severity” and to single sampling plans.
3. The AQL limits
The AQL limits appropriate for your market. If your customers accept very few defects, you might want to set a lower AQL for both major and minor defects.
Some specialized quality inspection software will show all the numbers automatically, but it is good to understand how to read the tables.
There are basically two tables. The first one tells you which ‘code letter’ to use. Then, the code letter will give you the sample size and the maximum number of defects that can be accepted.
First table: sample size code letters
If you follow my example, I assume your ‘lot size’ is comprised between 3,201 pcs and 10,000 pcs, and that your inspection level is ‘II’. Consequently, the code letter is “L”.
Second table: single sampling plans for level II inspection (normal severity)
Our code letter is “L”, so you will have to draw 200 pcs randomly from the total lot size. Besides, I assume you have set your AQL at 2.5% for major defects and 4.0% for minor defects. Therefore, here are the limits: the products are accepted if NO MORE than 10 products with major defects AND NO MORE than 14 products with minor defects are found. For example, if you find 15 products with major defects and 12 products with minor defects, the products are refused. If you find 3 with major defects and 7 with minor defects, they are accepted.
Note: in quality inspections, the number of defective products is only one of the criteria. It is sometimes called “quality”, or “quality findings”. The other criteria are usually on the inspector’s checklist, which typically includes:
- Packaging conformity (barcodes, inner packing, cartons, shipping marks…).
- Product conformity (aspect, workmanship…). If all the products are in red color instead of orange, there is no need to count each sample as a defect. It makes more sense to refuse for product conformity.
- Specific tests defined in the inspection checklist (they might not be performed on all inspected samples if they are time-consuming or destructive).
AQL Calculator
We usually help our clients to select the most suitable inspection levels and AQL limits, but you can use our calculator below (based on the AQL tables) to get a fast answer.
Fill in the calculator to easily find your perfect sample size (the number of pieces that should be randomly checked from the lot being examined) and the number of major and minor defects that can be tolerated based on your AQL specifications.
(This is based on the ISO 2859-1 standard, normal severity, single sampling plans only.)
The need for an objective measurement of quality
In certain product categories, there will be defective products in virtually every production batch. It is often true even after the manufacturer has checked each individual product and has repaired the defective ones since the visual inspection is not 100% reliable.
Therefore, in many supplier/buyer relationships (particularly when the application does not result in life or death outcomes), the supplier is not expected to deliver defect-free goods. The buyer needs to control the quality of purchased goods since he does not want too many defects. But what does “too many” mean?
How to set the limit between acceptability and refusal in a way that can be agreed upon and measured? This is when the AQL comes into play.
A look at AQL in more detail
As I wrote above, the ‘AQL’ is the “quality level that is the worst tolerable” on average over a period covering a number of batches.
In practice, three types of defects are often distinguished. For most consumer goods, the limits are:
- 0% for critical defects (totally unacceptable: a user might get harmed, or regulations are not respected, or the economic impact is catastrophic).
- 2.5% for major defects (these products would usually not be considered acceptable by the end user, for example the product does not work as intended).
- 4.0% for minor defects (there is some departure from specifications, but it is a small inconvenience and most users would not mind it — they might not even detect it).
These proportions vary in function of the product and its market. Components used in building an airplane are subject to much lower AQL limits.
Note that this tool is used mostly during final outgoing inspections (when the products are ready to be shipped out), and sometimes during production (when the number of products is sufficient to have an idea of the batch’s average quality).
If you really want to understand the concept of the AQL, you should spend about 20 minutes (total) watching this video on Youtube. Don’t forget to like and share it, please.
How To Read the AQL Tables for Quality Inspections (Random Sampling)
Or check out this article on how to read the AQL tables.
Special case: the AQL in the Codex standard stan233 (food products)
There is another widely-used standard for food products. It calls for taking a much smaller sample (which makes sense since opening a food product’s packaging means destroying it).
The general approach is the same, from what I saw, with some differences (e.g. the tables are different depending on the net weight of a unit of product).
Frequently Asked Questions about AQL
Questions about the general process of acceptance sampling
So, basically, I have to authorize the factory to produce some defects?
In theory no. That’s why the AQL was renamed, from “acceptable quality level” to “acceptance quality limit”. It is a “limit” (and a loose one at that).
Here is what the ISO 2859 standard says:
“Although individual lots with quality as bad as the acceptance quality limit may be accepted with fairly high probability, the designation of an acceptance quality limit does not suggest that this is a desirable quality level. Sampling schemes […] are designed to encourage suppliers to have process averages consistently better than the AQL.”
Note that, in practice, using these statistics means you assume the factory cannot reasonably be expected to turn out 100% good quality.
Alternatively, you can choose an “acceptance on zero” plan. As soon as one defect is found, the inspection is failed. But you can impose this on suppliers only in situations where quality requirements are very high (in the auto industry, in aerospace…).
As a buyer, should I charge back the value of the defective products to the manufacturer?
This is not standard practice. The standard practice is actually to charge nothing back, as long as the inspection is passed.
However, as the buyer, make sure to add this provision in your contract with the supplier: if an inspection is failed, the supplier has to sort & rework the goods, and submit them to a new inspection (and the re-inspection costs are charged back to them).
How to choose an AQL limit for my products?
I explained it in details in this article. It depends on your distribution channel and your product’s end use. Note that your supplier might refuse AQL limits they estimate as too tight (i.e. too low).
What are typical limits for consumer electronics?
A small company that doesn’t have much money to invest in DFM and the NPI process, in general, will usually set the limits at 2.5 or 1.5 (for major defects) and 2.5 or 4.0 (for minor defects). This should be communicated from the start, as it may have a direct impact on cost.
A company that invests a million USD or more in developing a new product, and that works with a contract manufacturer to prepare for large production volumes, will usually set a limit on major defects at 0.6 or 1.0. (source)
If I find too many defective samples, I have to reject the lot. However, what can I do to try and save the lot?
You can switch to 100% inspection and discard rejects.
You can also have a manager (on the buyer’s side) take a business decision – is it actually acceptable, even though the ‘quality result’ is not good?
In any case, don’t change the rules of the game (checking more samples by applying level III, going into double sampling), just to your purpose. This is not good. And it will send the signal to the supplier that your rules are negotiable or flexible.
What are the limits of a quality control approach based on random sampling and AQL limits?
A: There are several limits:
1. An AQL limit is a target rather than a maximum. The buyer might have a nasty surprise when receiving a batch of products that “passed” the inspection. Read more in this article.
2. A statistical QC approach does nothing to reduce the defects in the first place. Read more in this article.
Can’t I just do my own sampling plan?
Sure. If you have a math background, you know that you’ll need to use a hypergeometric distribution (since samples are taken from the lot at random, are checked, and not put back into the lot until the end of the inspection). Specialized software like Minitab can help you a lot here.
If you want to avoid statistics altogether, your limits on the numbers of defects will not make much sense, but they might “feel” right intuitively and it might make you more comfortable… Just be aware of their shortcomings.
Make sure you get the supplier’s agreement on your plan. This might be the hardest thing to achieve!
Is there a more efficient way of checking the quality of finished products?
There are many ways of drawing samples and checking their quality. If you don’t mind a more dynamic inspection plan, where the number of samples to check can’t be predicted in advance, you might want to follow a multiple-sampling plan or even a sequential sampling plan. On average, for the same confidence in the decision, fewer samples will need to be checked.
Is the concept of “AQL” only this one sampling standard?
No. For example, it is also in the Codex standard stan233 (generally used for certain food products). It calls for taking a much smaller sample (which makes sense since opening a food product’s packaging means destroying it).
The general approach is the same, with some differences (e.g. the tables are different depending on the net weight of a unit of the product).
What is the AQL standard? What is the AQL level? What is AQL sampling?
Can we also use this sampling standard to check incoming goods (components)? Or is it only for finished products?
We are setting different inspection levels for different parts of the inspection. When determining the acceptance of the entire lot, should we somehow combine it all to determine acceptance/rejection?
In principle, when it comes to counting defectives and getting to a pass/fail result, you should treat your inspection on level II as one inspection, and that on S-3 as a separate inspection.
It may all ends up in the same report, of course. But the results should come out separately. Then, if you have a pass on what you check in level II, but a fail on what you checked in level S-3, the whole report would logically be failed.
Can we have the same AQL limits for all products, if they all go through the same distribution channel, same customers, same ‘promise’ to customers?
Limits of 0 (critical), 1.5 (major), and 2.5 (minor) for the regularly produced batches of the same products if you have a good assurance that the underlying process is in control and the process & components are never changed.
In other cases, you need to be stricter. Limits of 0 (critical), 1.0 (major), and 1.5 or 2.5 (minor) make more sense.
Quality inspections based on acceptance sampling have been used for around 100 years. Is it still a valid approach?
Since the 1980s, there has been more focus on supplier management, process control, engagement and training of people, maintenance of equipment, and other ways to reduce the proportion of defects. It tends to work very well in a highly collaborative buyer-supplier relationship.
What did w. Edwards Deming, the famous statistician and “quality guru”, think about acceptance sampling in general?
However, his comments were written in the context of a company that aims are reducing the proportion of defects as close to zero as possible, typically a manufacturer that receives parts before processing them. He may not have written the same thing after looking at the realities many importers of consumer goods have to deal with.
Questions about the way the underlying statistics work
Why not just say, ‘we’ll check 10% of the quantity’, or whatever percentage deemed appropriate?
This is discouraged, as clause 4.3.3 of the ISO 2859-10 standard explains:
Ad hoc sampling should not be used because it will lead to unknown risks that may be too high. Furthermore, there is no formal basis for either the acceptance or non-acceptance of the lot. Examples of ad hoc sampling include the sampling of a fixed percentage of a lot or a convenience sample taken at haphazard times.
And here is one thing many buyers don’t realize. They say “inspect 10%”. But, as we go up in the total quantity, the proportion of products checked can decrease, for the same confidence in the inspection results.
As you can see in the chart below, if you follow the AQL tables, the number of samples to check (vertical axis) increases at a slower pace than the total quantity (horizontal axis).
Do we have to follow levels I, II, III, etc. and AQLs 1.0, 1.5, 2.5, etc.?
No. They are mere parameters that were thought to be applicable to most situations. For the sake of simplicity, it is better to have 3 tables with 10-20 columns each, than 50 tables with 100 columns each. Remember, all this was computed by hand in the 1930s, and inspectors had to look up the tables in paper form.
If you have a statistical software package such as Minitab, you can adjust the parameters as you see fit.
How to calculate AQL values?
If you have a statistical software package such as Minitab, you can re-do all the calculations and even adjust the parameters as you see fit. Some people have also done it in Excel.
If you deviate from the standard parameters, make sure your supplier confirms your new sampling plan & limits prior to any inspection work. You don’t want to get into a long justification after you reject a batch…
Based on my AQL, I calculated the proportion of defects authorized. Why don’t they correspond to the maximum number of defects authorized?
It is true. In our example above, 2.5% of 200 samples is 5 samples, but we accept the goods even if 10 samples are found with a major defect.
Why this difference? There are heavy statistics behind this issue. To keep it simple, the producer’s risk is his risk of rejection (based on the random element when drawing the sample) even though his products (if they were all checked) would be accepted. That risk is about 5% in this standard. And, along the same logic, there is a consumer’s risk and is around 10%. As you can see, this standard is favorable to the producer’s side.
What are the “reduced” and “tightened” severities?
They are designed to be used in very specific situations when a producer is particularly reliable, or on the contrary, fails too often.
In practice, these severities are seldom used. Most inspections are done in normal severity. The rules to switch from normal to reduced or tightened are considered an important part of the standard (actually the evolutions of these rules constituted the main changes from MIL-STD 105A and MIL-STD 105E) but can be ignored.
Jim Bossert wrote this in the Feb. 2016 issue of Quality Progress:
You can use any plan without using the switching rules, but you do run the risk of not meeting the alpha risk in the end. These plans were developed to be used, as documented.
A normal plan is generally used and the switching rules come in when the clearance number has been obtained.
Some processes may never switch. If you choose a plan that is tightened or reduced to start with, you potentially will either spend too much on inspection (tightened) or risk having a bad product go to the customer (reduced).
It is a business decision for you to make if your customer is not demanding it. The switching rules are there to protect the producer when the product is running well or it has problems.
What is NOT defined in the standard, and is free to be applied in different ways?
Several important things are not even mentioned in the ISO 2859-1 standard:
- How many cartons to pick (in case products are presented in master cartons, and the unit to check is the product). In most inspections, the number of cartons picked is the square root of the total number of cartons in the lot. Some companies request 2 times the square root.
- What the classes of defects should be. In most inspections, defective units can be classified as “critical”, “major”, or “minor”, and each company can define what is in what class. Some companies add extra classes: incidental, catastrophic, etc.
Special cases
If I find 3 minor defects on the same sample, should it be counted as 1 major defect?
The standard says nothing about this (or, more generally, about the way to count different classes of defects). So, this is up to your organization to decide.
One good way to think about it is, ‘is it a real problem if a consumer finds 3 minor defects on 1 product they bought?’ If the answer is “yes, definitely”, then count it all as 1 major defective unit.
What if we check the quality before the whole batch is completed?
A reader asked me about this special case. Production of 500,000 pieces is underway. An inspection is done when 10% of the production is ready. With a normal inspection level II, what is the sample size?
- 800 because total production is 500,000?
- 500 because pieces that are ready is only 50,000?
The short answer is, the standard doesn’t really address this special case, as it was primarily designed for an inspection after an entire batch has been made.
My practical answer is, go with this option:
- 500 because pieces that are ready is only 50,000
For further reading on this topic, feel free to check out all of my AQL posts and also read this detailed Quality Control basic concepts post here.
Need help with inspecting your production?
Get in touch with me by filling the form below and I will give you a tailored recommendation or quotation. My company Sofeast, can probably help you.
Get expert help to improve YOUR product quality from suppliers in China or Vietnam. Read: Quality Assurance In China Or Vietnam For Beginners
Grab your free copy of Sofeast’s eBook and learn the common traps new importers from China or Vietnam fall into, and how to avoid or overcome them in order to get the best possible production results. It also outlines a proven quality assurance strategy that you can follow in order to have better control over your product quality, covering:
- Finding Suitable Suppliers
- Defining your Requirements before Production Starts
- Don’t Skip the New Product Introduction Process
- Regular Quality Inspections (Trust but Verify)
- Tying Payments to Quality Approvals
Sounds good? Hit the button below to get your copy now:
*Editor’s note: This post was originally published in 2011, and has since been updated to include new information and formatting.
my question is this what is 1.5,2.5,4 etc. is this a percentage of faults. if yes than at aql 2.5 there should be 5 defectives allowed. while table says 7 allaowed. what is it ?
The reason is that the ISO 2859-1 definition of AQL is simply incorrect. The actual definition of AQL is the percentage of defective parts that is routinely accepted by your sampling plan. Thus, a particular sampling plan for an AQL of 1%, might actually only reject a lot if there are 2% or more defectives. What the 1% means is that if the true failure rate of your process is 1%, you will still, due to the random nature of your sample, get defective rates over 1% sometimes, however, 95% of the time, they will be under 2%. You can think of the actual number of defectives that a particular plan allows as the lower confidence limit of the AQL value.
Correction, you can think of the actual number of defectives that a particular plan allows as the UPPER confidence limit of the AQL value.
Yes I agree, the ISO 2859-1 definition of the AQL is confusing. That’s what I explain in the 3 videos I shot on this topic (see the links at the end of the article).
i would like to ask you from where you got AQL table and what is the document reference number of AQL chart?
ISO 2859-1 standard. There are other equivalent commercial standards in different countries.
Ghulam,
It is the percentage of defective products that the buyer is willing to accept in the total population of products.
Read the paragraph that starts with “Based on my AQL, I calculated…” above, and it will answer your question.
I want an Clear definition for AQL ?
Karthick,
The AQL is the worst quality level that the buyer is willing to tolerate.
how i decide the lavel of aql according to lot size
Mithun,
See the explanation below the 1st table, in the article above.
Thanks a lot .It was so useful for me.
please suggest the better system than AQL & why?
Praveen,
First, explain what you don’t like with the AQL system, and maybe I can make suggestions…
for plastic flexiable packaging, there are n number of major and minor defect. how we can make the list.
O.P.Singh Chauhan,
I am not sure I understand… What is the order quantity, and what AQL limits would you choose?
I’ve received a request to set an AQL level (which I had set at 2.0%) to:
“An AQL of 0.065 OR 0/1 reject/accept level”
I’m not particularly certain what this means…. I assume the 0.065 is just a much much tighter % than the 2% I had set (which is rather tight), but the “OR 0/1 reject/accept level” confuses me. Any idea on what was intended? Does it literally mean “0 rejects for every 1 accept” which would be an AQL of 0.0?
And by the way, good article. Many thanks.
Brian,
0.065% is much stricter than 2.5%. By the way, 2.0% is not in the tables, so you should not use this value.
“0/1 reject/accept level” means that the lot is passed if there is 0 defect, and rejected if there at least 1 defect. In practice it is similar to an AQL of 0.065%, except if your order quantity is above 150,000 pcs (I am assuming level II).
Very good practise in explaining the AQL and quality level concept.
In theory, if the sample size is 125 pcs in an order of 3000 pcs for level II.
Is it possible to inspect just 50 pcs or 80 pcs for some non critical portions of the product; like cosmetic of the product?
Daniel,
Thanks. To respond to your question: yes it is possible. See the special levels, on https://www.qualityinspection.org/inspection-level/.
What is the different between Special Inspection Level (S-1, S-2, S-3, S-4) and GenEral Inspection Level ( I, II, III )?. Do we need to choose either on or both must be choose?..
Aznal,
See https://www.qualityinspection.org/inspection-level/. Special levels are usually chosen for tests that destroy the product, or that take a lot of time (i.e. when you need a really small sample size).
In over 90% of cases, importers use general level II.
Hi,
what is the probability that i will accept a lot more than 1,5% defective if i use AQL 1,5 to inspect?
AdamH,
The standard does not indicate this probability… It is supposed to be adapted to a “normal” buyer/supplier relationship.
IF LOT QUANTITY IS 20 WHAT IS THE AQL
Ravi,
You can see on https://www.sofeast.com/aql-tables. Il level II, you should check 5 pcs.
I love how the majority of the comments are from Asians and South Asian named people. You would Google and searched for the meaning and definition of AQL is fantastic. Most people I work with who are Caucasoid couldn’t care less and don’t want to know frankly. The devil is in the detail as always you impress me.
Observer,
Yes, it’s funny. Lots of suppliers who wonder what their buyer is talking about, too.
Please also describe the method how did you calculate the 200 pcs of shipment samples for inspection if the shipment volume up to 3000-10,000 pcs ?
I appreciate your quality inspection tips.
S.Qaiser,
It is not a calculation. For the letter L, the inspector should pick 200pcs.
Look at the 1st and the 2nd tables in the above article.
thanks very much but i need more explain plz
Abdelaziz,
Not sure how I can help… Please be more specific.
Is there any AQL level 2.54 ?
Sanjay,
No. Nothing between 2.5 and 4.0.
Thanks for the information. Please advise which AQL we should apply to inspect handicraft articles (Metal Handicraft Items).
suggest critical,major and minor defects in floor covring goods (carpet,Bath mats,pitloom/fraloom rugs,Breided rug etc.
dear sir:-
i want to know according to A. Q. L.2.5 & 4.0 ORDER QUANTITY IS 1000 PCS
HOW MUCH CHECKED PCS IN 1000PCS
80 pieces out of 1,000 pieces, in level II (as explained in the above article).
Dear Renaud, please advise which AQL we can apply to inspect Metal Handicrafts items, as due to handicrafts no 1 piece is simillar to another, so how can we inspect as per AQL.
Sanjay,
You can certainly do like in the example of this article. Level II, 0/2.5/4.0.
Thanks for the illuminating article.
Is there any systematization behind the random drawing of the samples?
For exemple, I have a lot of 5,004 units divided into 139 master packages with 36 units each. Each of the masters contains 6 inner packages with 6 units in each inner. How will the inspector choose his samples? Since according to the table (based on level 2) he will need to inspect 200 units, does it necessarily means that there will be at least one sample from each of the master packages? Will the samples always be from the top inners or from the bottoms as well?
Thanks for you help.
John,
Interesting question. There are no indications about this in the standard.
Usually, here is the way it is done:
– The sq.root of 139 is between 11 and 12, so the inspector will pick at least 12 master cartons.
– He will take 16 to 17 pcs per master carton, and will make sure the total is 200 pcs.
– He will probably try to pick pcs in 2 or 3 of the inner cartons, inside each master carton. There is no rule for that, except that he should take some inner cartons from different parts (top, center, bottom, front, back…) of the master carton, and same thing for the pieces inside the inner cartons..
Hi Renaud,
Thank you for your prompt reply.
Is this somthing I should specify in advance to the company who preform the inspection? i.e. ‘you need to inspect at least X master cartons and at Y inner carotons from different parts’ in order to avoid a situation where all the samples will be picked up from the same places?
Is it common to determine this with the service provider when ordering the inspection?
Once again, thank you for your assistance.
John,
If you are working with professionals, no need to specify it.
i want to print out this page
if there is more than one defect on a garment, how is this counted
As the most severe defect found on that garment.
But make sure the description of the defect shows that there were several defects.
ANSI Z4, In the table, there are AQL of 100, 150, 250, etc. but the table reads that this number represents “Percent non-conforming and Nonconformaties per 100 items”. How can they be greater than 100 with that definition? Is it allowing for multiple non-conformances per unit?
I have a doubt about Mil-Std-105d Table for “Single sampling” plan for “Normal inspection” (Master table). If I have a lot of 100 units my sampling size code letter is “D” for S-4 Level, so sample size is 8 pcs, and if I apply 0.65 AQL there is an arrow down that goes for the acceptance criteria; 0 accept, 1 reject the lot, my doubt is; do I have to go down as the arrow shows and interpolate with sample size so then my sample size has to be 20 pcs, is that correct? can somebody help me!
The best is to inspect 20 samples and apply the [0,1] AQL.
But it is not an obligation, just a suggestion for the most purist among us.
It is fine to inspect 8 samples and also reject the lot if you find at least 1 defect.
Mr. Renaud Anjoran, please help!
Thank you very much for you opinion and help.
Another case; If I have a lot of 1500 units my sampling size code letter is “G” for S-4 Level, so sample size is 32 pcs, and if I apply 0.65 AQL there is an arrow up that goes for the acceptance criteria; 0 accept, 1 reject the lot, my doubt is; do I have to go up as the arrow shows and interpolate with sample size so then my sample size has to be 20 pcs, is that correct?
Same logic here. No need to check 32 samples — just check 20 samples and reject if you find at least 1 defect.
thanks behalf, If i have lot size 35,001 to 150,000 my samling size code is “N” for S-4 , so sample is 500 or 1250?
thanks behalf, If i have lot size 35,001 to 150,000 my samling size code is “N” for S-4 , if I apply 0.04 what is the sample 315 or 500 or 1250? some one help please
No, your letter is J for S-4 level, and you should check a sample of 80 pcs.
Adjust new AQL chart .For help us any student .Thanks.
There is no way to adjust it without corrupting it…
thanx i realy got my point understand
Ma Joe Gong
Thank you very much for your opinion
I want to know q’ty special inspection level s-1; s-2: s-3 and s-4, it’s same with 1Pcs, 2Pcs, 3Pcs and 4pcs?
No, it is not the same. The sample size depends on the lot size.
Does a Major defect also count towards the Minor defect count?
Using your above example (3,201-10,000, level II, 2,5&4), what if the result of the inspection was 9 Major and 13 Minor. Do the Majors also count towards the Minor total, for a total of 22 defects that are “at least Minor”? Or, are they always kept separate?
No. Better always keep them separate.
Better? Actually keeping them separate has funny consequences. If the minor defective allowance is exceeded a bit while the major/critical defect allowances still left some spare room, the AQL system would effectively recommend suppliers to smash a few products so that all allowances would be met again.
That’s right. Don’t ask me to defend that method’s logic… I am just explaining how it is supposed to be applied.
Although it seems like it, this is actually not right thinking. That`s because there might be totally different manufacturing mistakes that can lead to major and minor mistakes. So if you have found only 1 major defect and then more minor defects you cannot group them together since you might end up with a whole bunch of products having the same minor mistake. Then, although there would be only a few pcs of major ones the whole lot would become unacceptable by the end client. AQL has its flaws anyway, like any system i guess, and can be very unfair for the supplier or the buyer, (usually the buyer though). 😉
In the last time company, we keeping 2 point minor defects = 1 point major defect.
dear Mr Renaud,
Separate and not separate? is there any document write about this? pls share to me. If I choose not separate, Total is larger 14, I will reject it. is it right?
Sorry but your questions are not clear…
Follow your example, the second table , If I choose the lot size 200, AQL 2.5 and 4.0. I found 8 defects( AQL=2.5) and 8 defects (AQL=4.0). It mean total defect is 16.
Can I approve for this lot?
Yes.
Is there any benefit to performing the same inspection on the same lot?
Let’s say that my factory does a 2.5 AQL Level III inspection. Is there any benefit to having a 3rd party inspect the same lot at 2.5 AQL Level III after the factory completes its inspection?
Usually yes. The third party inspectors might be better trained, and will probably tell you the truth (they have no interest in lying to you, while the seller may have such an interest).
is the lot size refereed here is actual packing by supplier or is been refereed to P.O quantity. for ex : if p.O quantity is 1200 pcs & actual packing by supplier is 1210 pcs so how many samples i need to choose – 125 or 80 samples
The lot quantity is the actual quantity to ship.
Special case: if the supplier is late in packing and some pieces to be shipped are still unpacked, they are part of the lot.
If i am buying 100000 pairs of loge and coated on the pack aql1.5 so what does it men?
It means 1500 pairs defected?
Plz help me to solve the problem.
No, it’s a bit more complicated than that… You’d have to read the article above.
If i am buying 100000pairs of gloves and on the pack coated aql1.5 so what does it mean?
Does it mean 1500 pairs defected?
Plz solve my problem any one/
I don’t understand the question, sorry…
excellent explanation of what can be a complex concept. thanks
Thanks Gail!
Hi Renaud,
thanks, your explanation is very simply.
I have a question: are there values AQL internationally recognized for several items?. I would like to determine a AQL for the control assembly of the components of fittings nylon and aluminum. Thank you.
Yes, this standard can be applied on any products (finished or unfinished), instances of a process, etc.
But you should adapt the values of the AQL to your product and your market. Clck on the last link, at the bottom of the article, if you are wondering how to do that.
The quality plan submitted to our customer has been commented for Quantum of inspection as per ISO 2859 & they have not mentioned Lot size, Inspection level, & AQL level, Pl clrify What does it mean?
You can click on “QC basic concepts” in the menu of this site, and you will have some responses.
Lot size is the batch size.
What about a product that contains items, eg: I sell boxes of nails in packs of 100. For a lot size of 2000 boxes insp level 2 gives K, sample size 125 boxes defects allowed 10 and 14, now what happens if he opens the boxes and looks at the nails, are the defects still 10/14 or is our sample size to be changed to 2000×200 = 200,000 pcs? He would now have to inspect P/ 800pcs, 21/21?
Also the upper limit is 21, so 10 million pcs cannot have more defects than 500K pcs, does not seem fair?
Timbo,
I strongly advise you to consider that the lot is 200,000 nails, rather than 2,000 boxes. Count it all in pieces.
See https://www.qualityinspection.org/iso-2859-sets/ for more details.
Is there an exception to critical defects having an inspection that passes ? Or is it always 0/1
You mean, does it happen that buyers accept a certain proportion of critical defects? I can’t tell for sure, but it probably happens. It’s all up to the buyer (what is a critical defect, and what the limit for this category of defects is).
A very nice explanation, i would like to ask some question about AQL:
1. If I found 1 major and 1 minor defect on one unit, which type of defect is used, major (cause its greater than the minor) or count separately 1 major defect and 1 minor defect?
2. example lot size 281-500 with sample size 50, Major 1,0 (<=1) and minor 1,5 (<=2), during the sampling i found :
scenario sampling result : 1st unit found both 1 major criteria, and 3 minor criteria which means all type of the defect happens in one unit (accept or reject)?
1. Only count the major defect. Don’t count the minor defect.
2. Count 1 major defect only on that unit.
Note: what you call a “unit” should be the smallest selling/usable unit.
many thanks for your explanation, really helpful
Hi Renaud,
Are there any method that we can faster the Sampling process by reducing the sample size, and how is it performed?
When we can reduce to lower sample size, let say use G1? or when we also need to do higher sample size which is G2?
I also found some article that the sampling plan table, that the table have 3 types which are normal inspection, tightened inspection, and reduce inspection, how does it performed?
Sure, there are ways to do this. You can read this article: https://www.qualityinspection.org/reduce-man-days/.
Regarding normal/reduced/tightened: these are the different severities, not the different levels. More info on https://www.qualityinspection.org/statistical-inspection-levels/.
And a good summary of all these concepts is on https://www.qualityinspection.org/inspecting-less-samples/.
If we test 100% of our products, does this still applies? I’m guessing not unless I missed something.
No, this is only applicable if you do random sampling.
Hi, I am totally confused about dphu. Say I have a lot of 4000, sample size 200. I find 5 defectives and 20 defects. My understanding is I take (5*100)/200=2.5. What do I do with this #?
Thanks.
Good point. I answered it in the 3rd Q&A on this page, actually.
Sorry, but I do not see the answer below.
I mean, it is toward the end of the article. But I am also pasting it here:
Q: Based on my AQL, I calculated the proportion of defects authorized. Why don’t they correspond to the maximum number of defects authorized?
A: It is true. In our example above, 2.5% of 200 samples is 5 samples, but we accept the goods even if 10 samples are found with a major defect.
Why this difference? There are heavy statistics behind this issue. To make it simple, the producer runs a risk of rejection (based on the random element when drawing the sample) even though his products (if they were all checked) would be accepted. And, in the same logic, the consumer runs a risk of accepting bad products. The statisticians had to account for these risks, that’s why the numbers were adjusted and seem not to make sense.
what is the meaning of 0.25 ,0.65,1.0,2.5 AQL
Have you read the article above? It is basically the response to your question.
You need to give me more context…
Hello Renaud,
Let’s say an assembly line is producing 2000 products a day therefore sample volume would be 125, with ≤7 and ≤10 major and minor defects. However sampling all 125 at once is not practical and hourly tests want to be done. Let’s say 10 an hour for a 16 hour day to cover all options. Now does the ≤7 and ≤10 major and minor defects have to be totaled up for the whole day or can it be split up into the hourly tests in order to not slow down the assembly line. Also can figures be modified to fit the company, it is not a food product and safety is not of concern, just sending out a quality product however the defect limits provided on the AQL charts seem a little intense. Thanks
On a side note, products get shipped out randomly however they are packed 15 to a crate, would it be wiser to test each crate individually (lots size) at the 3 (sampling size), and 0 defects in order to have a greater control on the product quality.its still a 2000 production day but having the lot size as per crate, because tracking the products is of concern. (thoughts?)
A single-stage sampling plan is probably not the most appropriate in your situation. Here is what I would advise:
“Continuous sampling” is the best plan when products are made individually in a continuous flow. It makes no sense to pick samples inside each “batch”. It consists of several phases:
– At the beginning, each piece is checked (that’s the “screening”).
– After a certain number of pieces were found satisfactory, only certain pieces are checked randomly (that’s the “sampling”).
– If a piece is defective: back to screening.
Perfect thank you,
Is there separate AQL tables for this method or do you just choose numbers that fit your process, say screen 50 then randomly check 10 every hour. Also the company wants a paper trail would you advise to just record any failures during screening then record the random sampling ? thanks
Don’t worry about tables. This calculator will give you all the settings you need:
https://www.sqconline.com/mil-std-1916-calculator-acceptance-zero-beta?AVC=C
Hello,
If we have 1 item that is a 10 pc set, if we purchase as 1 pc, and we order 5000 10 pc sets, is the aql sample size based on 5000 sets or 50000 pcs (10pcs/set X 5000). Should we sample 200 sets or 500 pcs(which equates to 50 sets)?
Thanks,
Matt
Both are fine. Both have pros and cons. For example, when there are too many pieces in 1 set (and 10 is already on the high side), it loses its meaning.
I wrote an article about this on https://qualityinspection.org/iso-2859-sets/.
In the example you gave, they were not clearly. For ex: If I find out there are 18 minor defects and 5 major defects , so how can I judge this Po will be passed or rejected? In my experience, If the total defects are not over 24 defects and over 10 major defects this Po will be accepted to release. Is it right or not? Please kindly advice.
If the number of minor defects is above the tolerance, the overall result is FAILED. Even if the major defects are below the tolerance.
Hello Mr Anjoran,
Depend on your idea , which is the higher quality between the two cases I will give you
During the inspection with the same quantity as your example , 1st case: 18 minor defects, 6 major defects. 2nd case: 14 minor defects, 10 major defects.
Please advice and help me to judge which will pass the inspection.
Thank you!
If you decide to follow this standard and to set AQL tolerances, it can be very dumb. There is no need to look for logic in all the special caes. In some special cases it is just dumb. I am not defending this standard at all. I am just explaining how it works in practice.
Hi!
infact, During the inspection we will meet these situations and you must make the decision this Po will pass or not. The suppliers want to know this so that they will ship this Po or not. So you should list all the cases including the special cases, the examples which I showed to you are not special alot. the impotant things are that how could you convince the suppliers this or that order pass or fail the inspection. Sometimes, the minor defects are over the AQL but It will be passed the inspection. If the inspector can not make his or her decision on the orders he or she conducted . what will the suppliers thinking about the inspectors? the two examples I gave you , all passed the AQL , and the fisrt case the quality is better than the second. The total defects should not be over 24 defects ( the fisrt condition) and the major defects should not be over 10 defects ( the second condition). Anyway thanks for your document because there are alot of document are very usefull for the inspectors, I would like to remind you that when doing the inspection in practice the logic is very important.
Hello Mr Renaud Anjoran,
I read your documents I saw that they are very useful, however the examples you gave above are not clear alot. For ex: with the same quantity of this Po but If I find out there are 20 minor defects and 4 major defects How can I judge this Po will passed or not? In my experience working as an inspector , In my opinion If the total defects in this Po are not over 24 defects and the major defects are not over 10 defects . We will accept to release this Po . For ex: If you find out 11 major defects and 0 minor defects the inspection will be failed . If you find out 23 minor defcts and 1 major defect. the inspection will be passed. Is it right ? Please advice . Thanks so much.
Dear Renaud,
I’ve read this inspection information:
“Sample size: G1-20 for 1 item” And “Sample size: Major:50, Minor:32 for 2 items”
Is this method of choosing sample different from AQL?
Would you mind explaining for me this method?
Thank you!
An Nguyen
There not enough information for me to understand this sampling plan… “G1” might refer to “general level I”. That’s all I can guess.
Thanks for your response.
This is the document I’ve read:
For the 1st inspection, I guess you should follow level I.
For the 2nd inspection, it is not clear.
Hi Renaud,
I bought a robot recently (which is not delivery yet) and the company is writing the “Performance qualification (PQ)” document. This robot has 40 channels that dispense liquid in 40 devices at the time. The company has proposed to test the precision of the dispense on only 1 channel out of the 40 which I think is not sufficient.
I would like to know if this method can be applied to determine the minimum number of channel that have to be tested for precision in the PQ.
So, if I apply the process above, 40 channel with an inspection level II, the number of channel to test would be 8.
Let me know your thought.
Marc Pedneault
Marc, yes I think using the standard I describe in this article would be better than setting a number (such as 1) arbitrarily.
Dear Renaud, AQL 0.65.1.50 does it means: 65 major defect and 50 minor defect? what is figure 0 and 1 really means ? txs
Where did you find “0.65.1.50”??
can u tell me the formula to how to determine sample size, acceptance number and rejection number from the given population. (condition is without seeing the table, whether it is ansiz1.4 or different) tell me soon…
It is not a formula. You should read the above article, especially paragraph “Getting familiar with the AQL tables”.
Hi. We have lot size is 115pcs. We need to inspect base on level II. 1.5 major and 4.0 minor.so. how many sample size ??? 32 or 20pcs????. Bureau veritas QC got 32pcs to inspect.?? Why not 20???????please help to clear..thanks.
In normal severity and level II, the sample size is 20 pieces.
In normal severity and level III, the sample size is 32 pieces.
Hi,
Please i want to know how to have the value of acceptance and rejection of aql : 2%, 3%, 5% ?
and what is the method used to have this,and why these values of AQL doesn’t appear on standard tables?
thanks in advance
These values are not in the tables you’ll see everywhere. The statisticians arbitrarily chose some values. Remember that, in the 1940s, they couldn’t count on computers for easy calculations.
If you need to calculate values based on exact parameters of your choice, you can use the tools available on sqconline.com and use the calculator under “MIL-STD 105E”.
i have a lot of total 5500pcs, consisting of 5 different products of different qty. (item a = 2000PCS, item b = 860, item c = 1200, item d = 1440pcs)
Should the sample size based on the total qty of 5500pcs, or should it based on each product’s qty and count all the sample sizes separately for each item? The two ways make big difference in the volume of sample size. what is the correct way to do? pls advise
Though the QC will use AQL 2.5% / 4%, Level II, we have problems in defining how many function tests should be done, which requires more time and effort. like handle loading test, hardness test and performance cutting test. it’s impossible to test every sample of the sample size. which special level should we use (S-1 till S-4) if we use the special levels for certain function and performance test, can we still claim that our QC is in accordance with the AQL 2.5% / 4%, Level II? Pls kindly advise
The tests that are time-consuming or that destroy samples can be done on a smaller sampling size, right. And, in this case, you will still be able to say “we follow level II, with AQL of 2.5M and 4.0m” because these settings refer to the visual inspection.
I would say, go for 1 sampling (based on 5,500pcs) if you estimate that the defects that might appear are of the same nature on all 4 items. If not, got for 4 samplings.
For more info, see https://qualityinspection.org/sampling-plan-calculations/.
Can you please give some more information regarding the heavy statistics behind the disagreement between the number of accepted defective items and the actual percentages? My question is how the values on the inspection tables are eventually calculated. Thank you very much in advance for your help!
Unfortunately I am not a statistician. I suggest you ask a statistician if you want a clear explanation. It would take me hours of work to re-read the standard, try to grasp this, and put it in words — and it would probably not be 100% accurate.
Hello,
1 question about AQL levels on which I’ve never had a clear answer : I guess the level of AQL matches with a reiliability of probability. ex : AQL level 1 corresponds with 95% from the top of my head and it makes sense to have a higher reliability on higher level. Is there any corresponding table existing on leve 3, 2, 1, S4, S3, S3 … ?
Eric
That’s a very good question. That information is not told inside standard ISO 2859. And, from what I read, “hunches” and “intuition” played a big role in the definition of the standard.
Am I correct in saying that by choosing an AQL you aren’t
actually setting an amount as the maximum deficient? The operating curves for both sampling by
attributes and variables indicate that an AQL of 0.4% for example, will
actually accept a 9% deficient lot 5% of the time.
Correct. By setting an AQL you are setting a loose limit (kind of like a target not to surpass). That target is not the absolute maximum (you are right to look at the operating curves to have an idea about that).
From what I have gathered, I am going to explain my understanding – I’d be interested to see what you think about my conclusion.
I think there is far too much focus on the AQL in the discussion of sampling plans. AOQL (Average Outgoing Quality Level) and LTPD (Lot Tolerance Percent Defective) seem to be much better indicators of the accuracy of the inspection of a process. This picture, modified from MIL-STD-1916 attributes inspections, shows where these levels fall on the operating characteristic curves. The AQL, AOQL, and LTPD just represent different probabilities of acceptance, as I have noted on the chart.
Take the example sample size ‘E’ from the chart:
While an AQL of 0.5% might lead you to believe you will only be letting about 1 in 200 defects move through, in reality, the AOQL shows that you will be letting 2 in 200 through on average, with some lots having the potential of being as bad as 10 defects in 200.
Chart should be here now:
I don’t have that chart, but what you write seems to make sense.
If you send me that chart, I will put it up. My email address: ra (at) sofeast.com
I’m sure my impeccable picture posting skills really are boosting my credibility, but I can’t seem to get it to cooperate. There should be a standard OC chart with the several labels along the “Probability of Acceptance” axis:
95% — AQL
~75% — AOQL
10% — LTPD
The 95% and 10% are set by the definitions of AQL and LTPD.
The 75% is about where the average tends to fall with curves of this type.
is there a template on creating zones on a garment
Usually the buyer takes a drawing of the garment in question, and makes the different areas clearly visible. Then he numbers them, and applies a visual standard to each.
What is the apl of AQL in a dinning room ( Restaurant )
Not sure I can help…
Answer needed if the Customer determines that all lots are to be inspected, what would be the Five areas of determining an AQL?
Sorry but your question is not clear… What do you mean by “the Five areas of determining an AQL”?
Hi,
How to adopt the AQL into Oracle applications (ERP) Quality module, is there any way?
shaik
During a inspection based on APL should the inspector then check if the components are according to the Bill of Material (BOM)?
If you give the BOM to the inspector and ask him to check it on a few pieces, the inspector should do it. If you don’t give any such instruction, it is up to the inspector.
I always advise to clarify the inspection plan in advance…
I watched your video regarding “Consumer’s Risk”.
I have a question regarding “Producer’s Risk”.
In the Consumer’s Risk table it shows the percentage of defects you might find in 10% of lots which passed AQL. What do the numbers represent in the Producer’s Risk table?
Good question!
As you have probably guessed, the numbers are lower for the producer, since the buyer’s risk is higher than than the producer’s risk.
You can see them in the below image.
Dear Renaud,
thanks so much for running this blog – it is a very, very helpful read! I have one question in regard to defining the correct LOT (# of
homogeneous units) within the IQC environment:
According to my understanding, a LOT should be quantified by
“A defined quantity of starting material, packaging material or product
processed in one process or series of processes so that it could be expected to
be homogeneous”. The number of items in such a production lot forms the
correct base to size an AQL inspection sample.
Controversially, I see the practice that Chinese
manufacturers define the LOT size based on individual micro order quantities,
which are not linked at all to the above manufactured batch homogeneity, in
particular when the order sizes are small and only define the pull quantity for
a vendor managed inventory (VMI), the later stocked by an a.) independent and
b.) very different tact & batch definition.
Applying on such VMI pull lot size the AQL based sample
seizing approach must be wrong for the following reason:
• The VMI pull lot does not reflect necessarily the unconformity patterns of the
production batch, thus making any statistical derivations or statistical
statements in regard to sample robustness useless.
If above is correct, it would imply, that the right lot size
for AQL sampling should be either the production batch (optimal) or something
which is mirroring this production batch, such as a container shipment
reflecting somehow a sub-sum of homogenous production batch. Wrong would be a pull quantity, which is not
linked to the production process of one homogeneous batch of supplies, but more
to a stocking methodology, which can be rather unspecified.
I would be very interested in your statement to the
above! Thanks a lot, Philipp
Philipp,
According to the ISO 2859-1 standard, clause 3.1.13, a “lot” is a “definite amount of some product, material or service, collected together”. And they add this precision: “NOTE An inspection lot may consist of several batches or parts of batches.”
So I think you are a bit too restrictive in your approach.
But your general reasoning does make sense.
Dear sir,
which defects are 2.5 ? & which defects are 4.0 ? please give some advise.
Let’s say we have Critical, Major and Minor defects. Within Minor defects list we have flash, burn mark, sink mark, bubble, etc. If we set different AQLs for each of these defects (flash – 0.25; burn mark – 0.4; sink mark – 1.0, etc.) how do we establish if the lot is accepable or not? Do we need to meet AQL requirements per defect? or do we need to count all Minor defects together and make sure that the number meets lowest AQL from the entire list of Minor defects?
Thank you!
You should set limits for each category (Critical, Major and Minor defects). Then decide what defects go in what category. And finally you add up the defects you have found in each category.
can we do inspection for major and minor on same level as 2.5 % i.e. 10 defect each
Sure.
my field is bed linen production in huge bulk quantity . can u give tips on self quality management system to control required quality during production i.e cutting , stitching, checking , packing and shipment
Wow, that’s a pretty wide subject. A rough overview is on https://qualityinspection.org/increase-quality-china/ — but not all elements are applicable for producing linen.
Where is your factory based?
AQL IS NOT the “quality level that is the worst tolerable”. It is the ‘best case failure rate’, assuming you barely pass your inspection. Based on the table, for an AQL of 2.5%, the plan would allow 5% (10 out of 200) failures for inspection level II. Clearly, 2.5% is not the worst case when the plan allows 10 out of 200 to fail. The lower confidence limit of the failure rate (in the worst case) is the AQL. In the case of the two circled columns in the second table, the lower confidence limit of the allowable failure rates given are 2.5% (for 10 out of 200) and approximately 4% (for 14 out of 200). The conventional definition of AQL is completely misleading and totally bunk. I almost think it was deliberately designed to favor the producer (and mislead the customer) so that the originators of the tables could actually sell them to companies. Companies would then think, “Hey I can achieve and AQL of 2.5% with a failure rate of 5%. That great, lets buy those tables.” In reality, RQL is worst case, assuming you barely pass your inspection. RQL is the 95% upper limit of the failure rate (using exact CI) given that you just barely pass your inspection criteria. In any industry where the customer could be harmed by bad product, RQL is the only measure that should be used most of the time.
No, you are mistaken. There is a reason why an AQL of 2.5% actually results in accepting up to 10%.
If you want to learn more about this topic, watch the 3 videos I posted on Youtube (link at the end of the above article).
Regarding my previous question (or comment) you can email me at statbio.cg@gmail.com if you have an answer. I still think using RQL (or LTPD) is the best way to go. I’m sure you address that on one of your other pages. You can remove this comment.
I suggest you watch the 3 videos I posted on Youtube (link at the end of the above article). It should clarify the subject.
is any site i can visit and learn more about AQL?
Thanks
Hello, would like to know when we perform sampling checking, should the samples acquired be in 1 bag or few bags? Eg. Lot size is 1200 pcs which comes in 4 bags. Should I take the 32 pcs from the same 1 bag or from the 4 bags to make up 32 pcs? Pls advice. Tq.
The ISO 2859 standard says nothing about this, but there are general conventions in the inspection industry. Take the samples from at least 2 bags (square root of 4).
Tq Mr Renaud.
hello, let’s say that my supplier had a failure and i had to reject a lot of his items. after we looked for a solution it was decided that he will perform a 100% visual inspection on the items and only then will send them to me. now, i want to see that the corrective action was effective and want to perform an extensive visual inspection once i receive the product. what would you recommend? if the lot size is 500,000 will it be enough to inspect 25,000 pieces?
I’d advise to follow the standard I introduced in this article. I’d say you want to follow level II or level III (certainly not level I). And, if that supplier has already failed at least twice over the past 5 shipments, you want to follow a tightened severity rather a normal severity.
If I have Aql 1.0 what will be my confidence and reliability level on a single sampling plan where n=15, c=0? What is my LTPD?
You are mixing up two very different approaches (AQL vs. LTPD). They are not compatible.
Thanks for your articles, pretty much straight forward. However is the AQL approach being used for kilograms or liters. I think I’ve seen that liquids where not concerned. What about food? Could we inspect kilograms of powder or kg of apple dices for instance using the AQL? don’t know, something like I’ve 100kg of apple dices, I’m investigating 20kg of products and accept up to 1kg of major defects?!? Does not seem to fit. It does not apply to this, right? Is there an equivalent? Or shall I know the number of dices in my lot of 100kg for instance?
According to the previous post you’re answering very fast and since years, impressive!
Merci.
Hi Julien, I would estimate the average weight of a slice and then base calculations on slices. But there are no clear-cut rules about this. In theory, basing the calculations in kilograms or liters is OK, too.
i want asking about AQL table, why in the AQL table we did not found the i and o ? where is it?
thanks for your answer.
The i and the o? I don’t understand.
Maybe you mean 1 and 0?
Please, help me to clarify difference between AQL and AOQL ?
I ‘m working in one production company. Our supplier put AOQL % for critical, major and minor defects in in Quality Agreement. Material of that suplier is our incoming, raw material and I wish understand this AOQL term clearly. Please, clarify me
I am sorry but I am not familiar enough with the concept of AOQL.
Hi Renaud,
I have gone through your video but I still not able to answer my customer how AQL is defined and why there is a gap between AQL% and actual defect rate. e.g customer told me that he doesn’t want to accept a lot with >0.35% failure, but with AQL=0.25%, my customer is receiving failure rate at 0.5%.. Please help!!
Thanks.
Please remember what I wrote:
“I want no more than 1.5% defective items in the whole order quantity, on average over several production runs with that supplier” means the AQL is 1.5%.
–> 1.5% does not mean that, for each lot, the result is failed as soon as there are more than 1.5% of defects. It allows for variation from lot to lot, and tries to avoid rejection of a lot as long as the average of the lots might be under the limit.
Hi Renaud,
I have received a QA inspection report from our supplier based on AQL Level II and sampling Qty is 200. the inspection checklist contains 18 different measurments on each part and 5 test recorders for any of these 18 measurements. shouldn’t it contain 200 test recorders of any of these 18? Thanks
Not necessarily. 200 samples means the visual inspection is on 200 samples. But the tests that take a little longer are usually done on a smaller sampling size.
we are talking about measurements deviations around 0,2 mm and visual inspection does not work. so supplier can actually pick 5 samples out of 4000 Batch Qty and still hoping to capture some faulty units?
I can’t make a judgement because I don’t know what type of product it, made with what process, etc.
But, in some cases, checking just 5 pieces is sufficient to establish conformity (or lack thereof) without going more in depth, with a “reasonable” degree of certainty.
Note that, if you represent the customer, you are the party responsible for estimating whether this sampling plan makes sense. If you don’t specify this before the inspection, it means you delegated this judgement to another party, and protesting afterwards does not really make sense.
Hello, I am trying to implement an sampling plan where we have a batch size of 480, and a AQL of 0.25. For a batch size of 480 the general inspection level II code is H. This results in a sample size of 50 where everything must pass the inspection. When asked to explain what an AQL of 0.25 means, I said that an AQL of 0.25 means that if we pass our sampling inspection of 50 parts, then we can assume that the percentage of nonconforming parts in the lot is 0.25% (1 out of 400 parts will be nonconforming). Is that an accurate explanation?
On a slightly different note, one of my associates noticed that the AQL values go above 100, and actually go all the way to 1000 on my table. Does that mean at 100 you have 100% nonconforming parts, and what would 1000% mean? This led to confusion, and some apprehension of what the AQL of 0.25 truly meant.
No, I would not use this definition. You should say you want no more than 0.25% defective items in the whole order quantity, on average over several production runs with the same supplier.
Yes it goes over 100, for cases where several defects are counted on the same product.
Hi Renaud
Nicely done article and replies.
I have a question on zero acceptance sampling plans. They do not actually use AQL but rather the term ‘Associated AQL’. In the sampling plans above it is my understanding that an AQL of 1% would indicate there is a 95% chance of a lot containing 1% or fewer defects would be accepted (or a 5% chance of the same lot being rejected – producer risk). Using the OC curve you can determine the likelihood of rejecting other lots with higher or lower defect levels.
How do I make similar determinations on C=O plans?
I have Nicholas Squeglias book, but I am still struggling with an explanation. My suppliers are pushing for me to use the ANSI/ASQ plan but I prefer the C=0.
Thanks
Hi Kent, I’d recommend you watch this video where I explain these concepts: http://www.youtube.com/watch?v=8bUe8nQpI0s.
Hi Renaud,
I would like to share with you my case. I have an order of 1200 pieces.
My AQL define 2 check lists
1. Visual check / level S-4 ==> I have to control 32 pieces in visual
2. Functional check/ level S-2 ==> I have to control 8 pieces in functional
Question1:
I have to pick from the carton boxes 40 pieces right? (32+8 = 40)
Or
Can I select just 32 pieces and then inside 32 pieces, I will take 8 pieces to control the functional? What is the right way?
Case2: Visual check / level S-4 ==> 32 pieces in visual with Maximum 3 minor defects and 1 major defect
Question2
If I control 1 piece (the first piece), I found down in this piece, there are 4 minor defects and 2 major defects in visual. (in ONLY 1 piece)
==> It is out of our tolerance of defects==> Not ok. No need to control more. Order failed! Is it right?
OR ==> I count it is 1 defective with 1 major defect
I continue the 2nd piece and my level of acceptance is reduced to 3 minor defects and 0 major defects
So we count the defects Or defective?
Thank you for your advice
Here are my responses:
Question 1: you can pick just 32 pcs.
Question 2: you just count 1 major defect. Count the defectives.
Thank you so much. Nice day!!!
I wrote many things and it got me error 405…well I’ll do it again.
First of all, thanks for the article it was a really good explanation but as my english is not so good there are things that I couldnt understand quite well.
Well, in early 2015 I am going to open a chinese company branch in Brazil and I have to do inspections of the pcs based on the AQL, right?
Well they told me that the AQL is 0.4 but in the table that you posted on the article there is no AQL 0.4 so or they wrote it wrong for me and they meant 4.0 or is there an AQL 0.4 ?
Is there any document or article that defines what are the major and minor defects of a product or is it up to the company to decide it?? I’ll be producing equipments for health quality and stuff like that, as they are health/medicinal equipments if there any document or article that defines the defects?
Another one that I couldnt understat quite well, In the exemple that you gave in the article above, you show AQL 2.5 and 4.0 and you set 2.5 for major defects and 4.0 for minor defects, do I have to choose 2 AQLs or can I just set AQL 4.0 for both ? If I can set it with 1 AQL for both in 4.0 (for example in Level II / Code L) I would have to inspect 200 pcs and in there I could have 14 or less pcs with defect, right ? But as I set both (minor and major) defects on AQL 4.0 I could have 14 or less pcs with major defects AND 14 or less for minor defects? Or is it 14 or less of ALL?
If you could send me an article or a document with a simplyfied explanation, I think it would help me.
PS : Sorry for my bad english, as I am a korean and I lived in Brazil since 1998 my english is not so good.
Best Regards,
Suk
0.4 is not among the “preferred AQLs”, so it is probably a typo.
It is up to the buyer to decide what constitutes the different classes of nonconformities (major or minor) and the AQL for each. The AQL for each can be the same, if deemed appropriate.
Sooo what you’re saying is that if the AQL is the same for both minor and major defects, I don’t need just < or = 14 (in case of 200 pcs ) for both of them ?? it would be a total of 28 pcs??
If the AQL is the same for both minor and major defects, the inspection is failed is 15 or more defects are found either in the minor or in the major category (or in both).
If you can be more clear, if we inspect 200 pc and find 11 major and 6 minor is that a pass or fail?
in other words are they allowed 10 major and 14 minor on same 200 pc?
if more than 10 major alone is it a fail ?
if more than 14 minor alone is it a fail?
what about 7 major and 10 minor is that a fail?
In that case (you find 11 major and 6 minor), it is a fail.
Yes they are “allowed” 10 major and 14 minor on same 200 pc.
7 major and 10 minor is passed.
Hi, I want to know that how i do AQL in my footwear company, Please advice
You mean, you are a producer? Maybe you want to have an outgoing inspection plan that mimicks a buyer’s random inspection. Is that your idea?
Please explain what is the AQL calculation formula. EG: 2.5% /0.65%/ 1.5%
Unless you want to use a hypergeometric distribution in Excel, I strongly suggest you watch the video I posted in the article above. It will explain how to get to the values you want, with no calculations at all.
How would random selection of samples be done from Tape and Reel Packaging for Electrical Components of your example?
If one could assume the items were packaged in random from bulk, the first 200 would be ok?
If Serialized, probably not… What should be the sample size ?
Thanks,
If you inspect them after they are in a reel/tape, there are several approaches:
– Follow the statistics based on the number of component — that’s the ideal approach if, in subsequent production/use, you’ll count the defect rate as a % of components. But that might be inconvenient for picking the components on this reel, that reel, etc.
– Do it based on the number of tapes/reels — probably not the best.
– Follow a plan closer to that of fabric inspections — see https://qualityinspection.org/inspection-of-fabric-rolls-in-china/ for inspiration.